In industries such as manufacturing, chemical production, and semiconductor processing, vacuum pumps are critical power equipment, and their efficiency and lifespan directly impact the stability of production lines. As a key protective barrier for vacuum pumps, the performance of vacuum pump intake filters significantly affects their ability to filter dust, particulate matter, and corrosive media. Addressing industry pain points, our next-generation vacuum pump intake filters stand out with customized design, high-temperature and corrosion resistance, and reusability, providing global customers with efficient and cost-effective solutions.
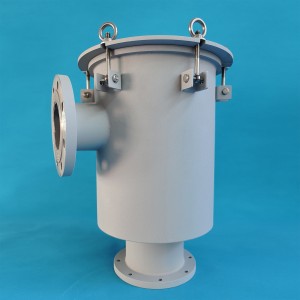
Core Selling Points: Precision Adaptation for Reliable Protection
- Customizable Flange Interfaces for Global Compatibility
Different brands and models of vacuum pumps have varying requirements for intake flange specifications. We offer personalized flange customization services, as well as precise machining based on customer drawings. This design not only simplifies installation but also ensures a tight seal between the filter and the vacuum pump, eliminating air leakage risks and ensuring stable operation. - Stainless Steel Filter Element: Durable Protection for High-Temperature and Corrosive Environments
Traditional filter elements are prone to deformation and degradation in high-temperature or corrosive gas environments, leading to filtration failure. Our filters use high-quality stainless steel (304/316) filter elements, capable of withstanding temperatures up to 200°C and resisting corrosion from acidic, alkaline vapors, and organic solvents. The unique woven structure ensures mechanical strength while maintaining excellent gas flow, making it ideal for demanding applications such as chemical processing, electroplating, and high-temperature heat treatment. - Low-Precision Design: Balancing Efficiency and Maintenance Costs
To meet the core requirement of intercepting large particles and protecting the pump, our filter elements are designed with relatively lower precision (10-50μm). This optimization avoids excessive pressure drop and energy consumption caused by high-precision filters while effectively capturing impurities that could damage the vacuum pump impeller.
Applications: Empowering Diverse Industries
- High-Temperature Environments: Such as plastic injection molding and metal smelting, where the filter stably intercepts dust and molten particles in high-temperature gases.
- Corrosive Environments: Suitable for filtering acidic gases in chemical plants or purifying volatile media in electroplating workshops.
- High-Frequency Usage Scenarios: Industries like food packaging and printing machinery, where frequent vacuum pump start-stop cycles require washable filters to minimize maintenance time.
Why Choose Our Vacuum Pump Intake Filters?
- Flexible Response to Needs: Customized production from flange dimensions to filter materials, with samples delivered within 7 days.
- Optimized Lifecycle Costs: Low initial purchase cost and a filter lifespan of 1-3 years (depending on working conditions).
- Global Service Network: Technical consultation, installation guidance, and rapid after-sales support to ensure peace of mind.
Take Action Now and Customize Your Vacuum Pump Protection Solution!
Whether you need to adapt to special flange specifications or tackle extreme working conditions, our engineering team is ready to provide one-on-one technical support. Click to inquire and receive a tailored product solution and quotation. Let our high-performance filters safeguard your vacuum pump system!
Post time: Mar-01-2025